Optimising Warehouses Through Storage and Automation Combinations
Share
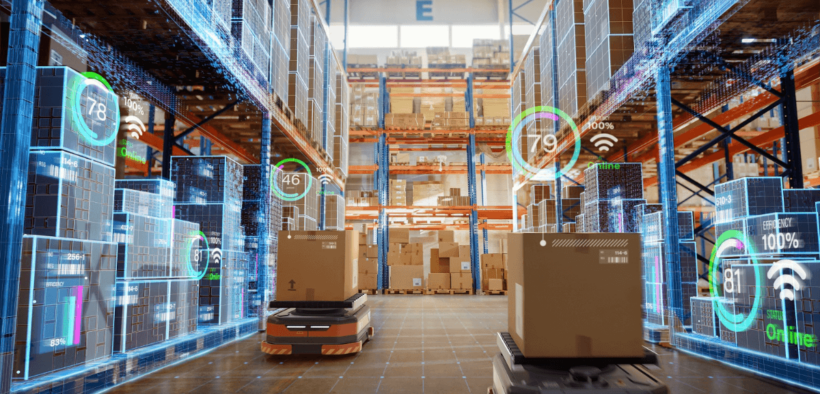
Operating a highly efficient warehouse requires multiple solutions as manufacturing and warehouses evolve. The focus has long been on technology and the implementation of Warehouse Management Systems (WMS). Now those same technologies must integrate through cloud computing and analytics across several different software packages to manage robotics and other operational tools.
The warehouse floor area is impacted by the need for increased returns on not just square meterage but cubic square meterage. Companies are looking for solutions to handle larger volumes of goods and inventory using every available space. The traditional laneways between pallet racks for stock movements are under scrutiny for the space they use. Different racking combinations and changing materials handling equipment are leading the shift from traditional racking design.
Optimised warehouses incorporate technologies, warehouse racking design and automation.
Integrating robotics for semi- or fully automated facilities is central to design considerations. This is led by the drive toward the next phase of the industrial revolution, Industry 4.0.
This new revolution is characterised by increasing automation and the employment of smart machines and smart facilities. Informed data assists in producing goods and managing inventory more efficiently and productively across the value chain. There is also a requirement for environmental design considerations to reduce energy costs that continue to rise and affect the profitability of warehouse operations.
Today, the company warehouse layout design considers the facility’s degree of automation and robotics. Warehouse designers look at where cubic square meterage can be optimised and the reduction of human interaction to manage inventory and how you can efficiently manage energy costs.
To address the cubic square meterage, the rising use of high-density automated storage and retrieval systems create an efficient, reliable, fast inventory movement system with excellent use of the facility space. Operated through a pallet shuttle on specifically designed deep lane shelving systems removing the need for manual material handling. The traditional lanes between racking are now storage space accessed through shuttles increasing the use of cubic square meterage.
The pallet shuttle system storage and retrieval system loads and unloads inside the shelving system in a similar style to the manual drive-in or pallet-flow set-up. The shuttle can operate on one or more main aisles moving inventory to the correct storage channel and racking position. The high-density storage eliminates the need for driving aisles, providing a marked increase in storage capacity. Contained in deep lane storage, the retrieval system increases the productivity of your facility. In addition, you can operate multiple shuttles within the racking.
The extended range of standard high-density racking profiles allows an optimised and economical design for many projects. In addition, it provides flexibility for warehouse layout, pallet sizes, and pallet weight.
This high-density storage system can be applied in semi and fully automated warehouses in environments ranging from -25°C to +45°C. It is ideal for cold storage environments and warehouses requiring a high level of inventory movement continually.
For Industry 4.0, the shuttle traffic is handled independently by its software. Orders are issued from your WMS to the local warehouse control system, which selects the shuttle to perform the specific task and determines its optimum path. The occupancy rate of the various storage lanes, the status and operation of each shuttle and an overview of all performed tasks can be consulted on the software and transferred to your main system.
The self-powered pallet carrier transports pallets on both the rails of the storage lanes and the rails of the main cross lanes. The so-called cross lanes or intersections between the storage and main lanes are designed for a smooth transition of the shuttle when changing direction.
As higher energy prices prevail, energy consumption and efficiency are essential considerations in warehouse design. This includes the energy consumption and efficiency of your integrated systems, not only the building itself. Energy consumption in warehouses is mostly related to the operation of handling systems. With a high density system the need of lighting in the warehouse is now only required in areas where personnel are operating. The rest of the warehouse lights remain off.
Warehouse design must consider all these elements to provide scalable solutions as companies shift to semi-automated and fully automated environments. The maximisation of cubic square meters and lowering of energy consumption. If you want to improve your warehouse’s performance, please reach out to Bowen Storage.