Collaboration is key to beating supply chain issues in manufacturing
Share
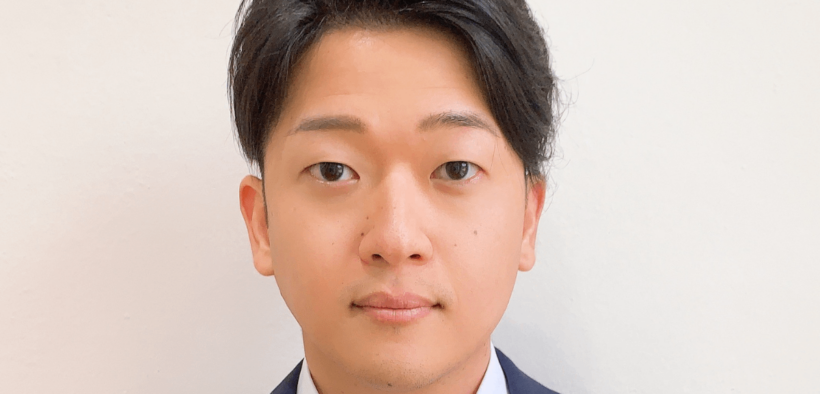
Universal Robots’ Country Manager Masayuki (Masa) Mase explains why collaboration is key to overcoming ongoing supply chain issues in manufacturing.
Reports of ongoing supply chain issues from manufacturers in both Australia and New Zealand are expected to last well into 2023. This, coupled with labour shortages and equipment availability, heeds uncertainty.
“These factors impact on profit, customer satisfaction and ultimately, on a company’s ability to compete,” explained Masayuki (Masa) Mase, Country Manager for Universal Robots.
In the case of Universal Robots, the availability of parts is crucial.
“One cobot typically comprises around 600 different parts – sourced from more than 100 separate suppliers. If any of these parts were to become unavailable, we would be unable to complete production,” Masa said.
In a challenging landscape, Universal Robots has seen significant growth in production while fulfilling its production plan.
During or throughout this time, the company said it has succeeded in delivering cobots within typical lead times, despite global shortages of key components and ongoing delivery issues.
Compare this to the market average, where it is not unusual for delivery to take four months, and it is especially impressive.
You might wonder what the recipe for success is? Well, the answer is simple: collaboration across the supply chain.
Factors to overcoming supply chain issues
“Several key factors come into play to make collaboration possible. This simply doesn’t happen overnight,” Masa said.
He shared four key factors that Universal Robots applies in its business to achieve effective collaboration:
1. Commitment to relationships
Universal Robots’ production team is 150 people strong.
“Each person plays a role in ensuring that cobots are manufactured and delivered on time,” Masa said.
Many of these individuals are specifically tasked with overcoming the company’s biggest challenges, including supply chain issues.
“This is where relationship building comes in. The stronger the relationships, the better the collaboration. Together, we can problem solve to anticipate and overcome any potential delays,” he exlplained.
Vice President for Operations and Supply Chain, Anders Lassen added that “the emphasis is on keeping everyone aligned to the shared goal – namely, the timely delivery of cobots to our customers.”
2. Remaining agile
Universal Robots said its focus on collective effort is aligned with ‘out-the-box’ thinking to find solutions to problems.
There is an inherent embracing of innovation, with a disruptor mindset that allows for an agile and rapidly adaptive approach. This culture of trust and collaboration also relies heavily on close ties with the R&D teams as products sometimes need to be altered based on the components that are available, without compromising on quality.
3. Ensuring that contingency plans are in place
“Planning for every hypothetical situation ahead of time ensures that there are no delays,” Masa said.
“So often, companies are caught in the crux of the situation with no ‘plan Bs’ in place. Having an approved plan in place before a crisis occurs saves a lot of time and hassle,” he said.
4. On-time delivery
The timely delivery of robots is a high priority for customers – particularly in a business environment characterised by fluctuating demand and uncertainty. Short delivery times mean companies can transform their operations quickly and see results within weeks rather than months.
“At Universal Robots, we are committed to our customers’ success, and we deliver on our promises. This helps to build trust and respect,” Masa said.