How to be a successful leader in the future of supply chain
Share
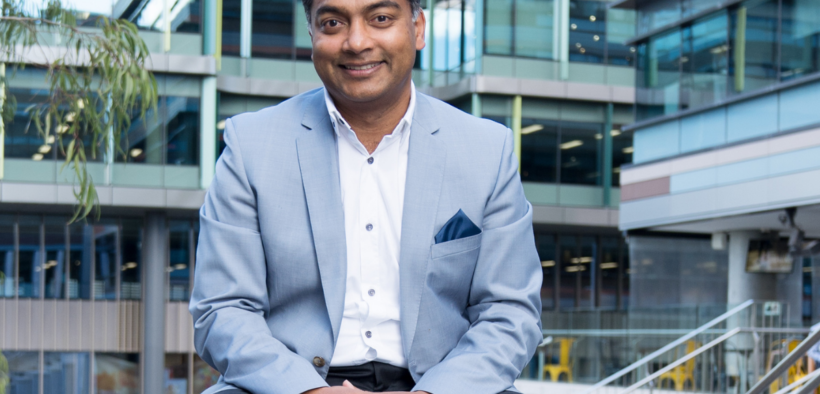
Operational Excellence expert Ishan Galapathy gives his insights into how supply chains have evolved and how organisations can gear up to become leaders in the future of supply chain.
In 2013, I visited the world-class Pringles mega-factory in North America. The 40-acre under-roof factory was then owned by Proctor & Gamble (P&G). It was an opportunity to understand the systems, processes and disciplines required to run the day-to-day operations and the year-on-year performance improvements. Even among the global P&G sites, this factory was one of the best—it fell into their top 10% global sites by their own standards.
P&G is no stranger to world-class supply chains. In Gartner’s annual global top-25 supply chain rankings, it is one of five companies (alongside Amazon, Apple, McDonalds and Unilever) to be classified as ‘masters’—a title given to companies that have held a top-five ranking for at least seven out of the last ten years.
I’ve been studying these world-class supply chains to understand how they operate and lead. The trends and benchmarks they set motivate other companies aspiring to operate in a world-class manner. Below are three broad evolutionary categories of supply chains. Understand where you are right now and explore what is required to be a supply chain leader in the future.
THEN: Focusing on the Day-to-Day
During the industrial growth period following World War II, businesses leveraged technologies of the second industrial revolution (assembly lines and factories powered by electric motors) to increase output while reducing costs.
Management-by-hierarchy with command-and-control leadership styles primarily focused on unit cost. Supply chains were an opportunity to squeeze costs out. Mass assemble lines pumped volume, which was pushed through the supply chain channels to the customer. Vision and mission statements spanned across walls.
It is not uncommon to still find companies still stuck in the day-to-day chaotic vortex and operating with this outdated mindset and model.
NOW: Focusing on the Year-on-Year
Many companies today are trying to catch up with the maturity levels I observed at Pringles in 2013. We are moving on from vision and mission statements to purpose and value. Strategies and tactics are created to bring the purpose to life. Employee engagement is highly valued, and many are trying to reverse the damage of the previous ‘then’ era, where employees weren’t given a voice. Women in supply chains are recognised as a way of demonstrating the company’s diversity policy.
Identifying machine losses and structured problem solving have become the competitive edge, not only to reduce costs but to unlock hidden growth opportunities. The advancements in computing and robotics are making it possible to improve quality, increase capacity and reduce costs simultaneously. Total delivered costs are taking priority over unit manufacturing costs. Workplace safety scope is expanding to include environmental factors, and with rising energy costs and global themes such as carbon footprint, companies are focusing on reducing energy consumption and environmental impact. Sales and Operational Planning (S&OP) is bridging the gap between demand and supply as supply chains are moving towards a pull model, reducing warehouse inventory holdings.
NEXT: Focusing on the Decade-upon-Decade
To lead into the future, we need to think farther ahead than year-on-year and 3–5 year. The definition of supply chain is changing from the standard make-and-move model to include demand planning, new product introductions, procurement, network designing and change management. Digital transformation is driven purposefully to balance people and processes, and tech is not introduced just for tech sake. Industry4.0 technologies such as augmented reality, virtual reality and 3D printing allow for improved customer experience with smart labels on products and mass customisation. Supply chain is a growth enabler and supporter.
Diversity is moving beyond women in supply chains to include disability, and board rooms have moved away from pale-male-stale executives. Purpose and values are passed onto suppliers and customers. We’ve evolved from carbon-neutral to circular economy. Regeneration of agricultural fields and funding education in developing countries is considered socially responsible. Agility to identify, pilot and implement trends, market needs, and opportunities are standard.
In countries such as Japan, companies even talk about generation-to-generation, but the western world isn’t there yet. The sooner we leave the day-to-day paradigm, the quicker we can begin the pursuit to world-class excellence. Excellence is both a journey and process: start it, support it and sustain it.