Supply Chain Leaders Must Design a “Fit for Purpose” Organisation
Share
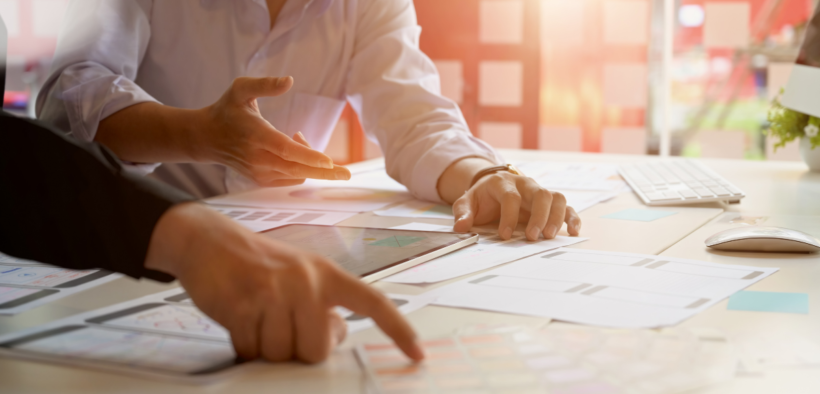
Supply chain planning leaders that define their function’s “fit for purpose” and choose a corresponding organisation design will improve their results and be better aligned to the overall business, according to Gartner, Inc.
The term “fit for purpose” describes an approach where planning leaders focus on what they should be doing, instead of benchmarking what others are doing, but may not necessarily work for them.
“Many supply chain planning leaders ask themselves if they should organise their function in a more centralised or decentralised way,” said Ken Chadwick, Vice President Analyst with the Gartner Supply Chain practice.
“To answer that question, they must first understand what their individual fit for purpose organisation looks like,” Chadwick said.
To design a fit for purpose planning organisation, leaders must consider their companies’ business and operating model as well as the operational mindset.
Business and Operating Model
The first element of designing a fit for purpose planning organisation is to understand the business and operating model of the overall company – customer base, products, serviced markets – and determine to what extent those factors are changing.
According to Ken Chadwick, some companies are now moving from global to more regionalised supply networks because global networks are less resilient when it comes to disruptions, such as trade wars or the COVID-19 pandemic.
“On the other hand, there are companies that want to try a more centralised approach to better serve their key customers,” he said.
Operating Mindset
The next step is to focus on what is important to the company in operations and decision making. Some companies’ mindsets focus on business unit accountability, so they align planning to a commercial leader who owns those outcomes. Other companies are driving an end-to end mindset, leading to one integrated planning organisation serving enterprise outcomes. Mindsets related to cost-focus, customer experience, innovation, agility, resilience, and risk also have a significant impact on how planning leaders organise.
“When planning, leaders know about their organisation’s present and future operating model and mindset, they can in turn think about what their own function should look like to best fit in and serve its purpose,” Chadwick added.
Decentralised, Center-Led or Centralised
Based on the organisation’s overall operating model and mindset, supply chain planning leaders can evaluate if a decentralised, center-led or centralised model is the best design for their function.
In a decentralised model, all planning roles report into the separate business unit leaders. This approach makes sense for large portfolio companies with mostly independent business units.
The center-led model leaves planning operations within the business units but creates roles at a global level that focus on planning processes and long-term planning. Finally, in the centralised model, all elements of supply chain planning report into an integrated planning leader who is running all aspects of planning across the different regions.
Ken Chadwick concluded that there really is no one-size-fits-all solution for a planning organisation, nor is a decentralised model necessarily a sign of lesser maturity. He said planning leaders must evaluate their individual situation and future plans and design their function accordingly.
Source: Gartner Inc. newsroom