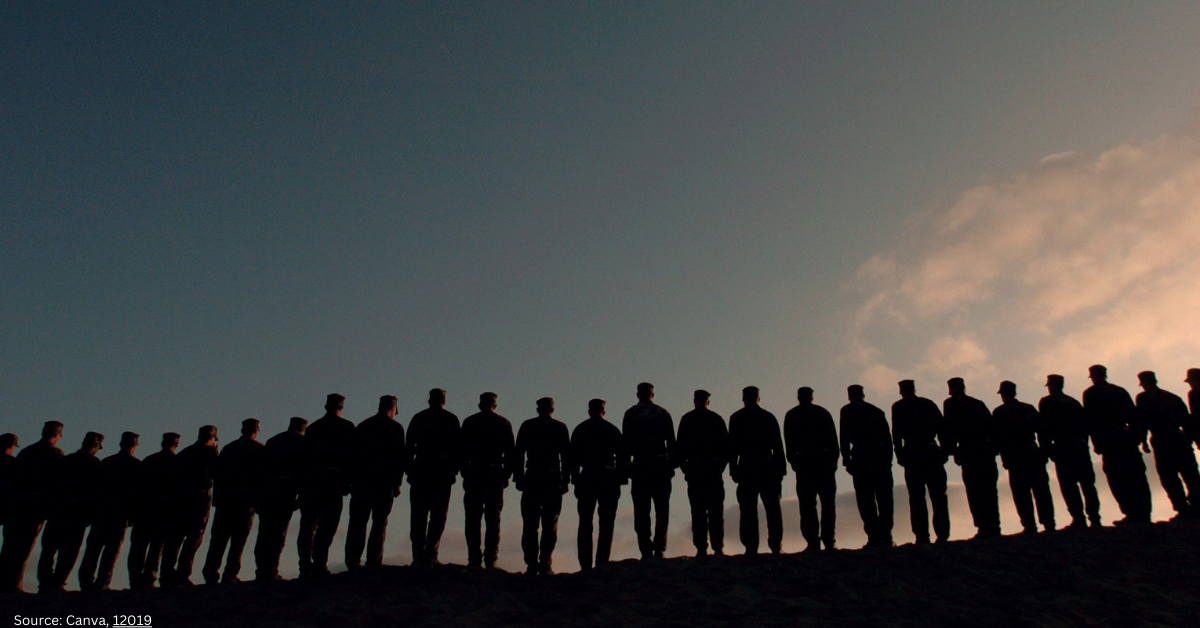
The primary objective of any warehouse operation is to maximise margins, and using an Automated Storage and Retrieval System (AS/RS) can save money by reducing labour costs, accelerating throughput, and increasing capacity.
When companies are considering automation, the two important questions companies ask themselves are:
When it comes to the capital expenditure required to invest in warehouse automation, these two concerns frequently cause warehouse managers to have second thoughts. However, your journey towards automation does not need to occur all at once; it can be a gradual process.
Let’s look at how you can accelerate your ROI.
The accelerated ROI of automated storage and retrieval systems can be attributed to examining all cost-saving sources versus traditional storage systems. This accelerated ROI makes sense when considering saving on expenses and capital expenditures.
A major factor contributing to the value of your investment and ROI is that machines never get tired or slow down. You can extend operating hours to 24 hours per day, seven days per week, accelerating the return on investment for warehouse automation.
These are some of the other key factors and benefits responsible for warehouse automation’s ROI.
1. Increased storage capacity
Automated storage systems, especially vertical lift modules, store significantly more items per unit of floor space than traditional shelving systems (up to 90 per cent less floor space is required). These space savings has assisted many companies in needing to relocate their premises and avoiding the capital expenses of relocation.
Frequently, manufacturing and warehouse spaces are not optimised, resulting in significant space loss. A functional layout combined with AS/RS can assist businesses in operating effectively. Moving items from one location to another within a facility is an expense that does not add value and may cause the products to be damaged. This option for high-density automation provides inventory storage capabilities and increased capacity.
2. Enhanced effectiveness
The use of warehouse automation and robotics genuinely impacts labour efficiency, process accuracy, and overall productivity and is no longer merely a futuristic aspiration. Consequently, automation is becoming a competitive necessity for businesses of all sizes.
Contrary to popular belief, size is irrelevant in this instance because the solutions available are extremely flexible and scalable. A small business may be advantageous because it can acclimate to change quickly. A further advantage of scalable solutions is that they enable smaller businesses to test out expansion without the associated risks.
3. Energy conservation with AS/RS
Due to a reduced overall footprint, a warehouse’s heating, cooling, and lighting needs can be diminished, resulting in cost savings. These costs are especially significant if you are storing frigid or perishable items.
4. Productivity increase
Happier employees are more likely to be productive. For this reason, an increasing number of businesses are automating their warehouses to reduce over-exertion and repetitive tasks, thereby reducing safety risks, lost productivity, excessive walking time, and employee turnover.
Manual selection is time-consuming and laborious. Constantly rising expectations for greater pick rates and lower error rates put pressure on employees. Automating the order-picking procedure can assist you in moving quickly through the line. The most effective solutions can be customised without requiring months of downtime or a lengthy delay for warehouse automation ROI. By automatically bringing an item to the operator, instead of requiring the operator to search for it on a shelf somewhere in the warehouse, retrieval periods are reduced to a fraction of the average.
5. Improved selection rates with AS/RS
Human errors are inevitable in conventional warehouses, where workers use printed lists to pull dozens of items from shelves daily. Delivering the incorrect item to a client is a costly error that results in lost time, additional delivery costs, and a dissatisfied consumer. With laser pointers, alphanumeric LED bars, put-to-light systems, and other similar aides directing operators to units and quantities to retrieve, automated storage and retrieval systems virtually eliminate incorrect picks.
6. Labour forces enhancement
Warehouse operators continue to report having labour recruitment challenges. For this reason alone, many companies are now looking for automation solutions to resolve their labour shortages. Industry studies have demonstrated that AS/RS can increase workforce productivity by as much as 85 per cent because a single employee can perform the same amount of work that previously required multiple operators.
Employees enjoy working with automated solutions as they do not spend all day retrieving items by stooping or ascending ladders. As a result, employee turnover tends to be reduced too. And because the devices are simple to operate, highly qualified candidates are not required to operate them.
To conclude: An accelerated return on investment for automated storage and retrieval systems is achievable. Depending on your warehouse functions, you could realise an ROI in six to eighteen months.
To discuss your warehouse automation requirements, please connect with us at Bowen Storage.
Follow us on social media